L'inventaire en tant que conséquence - Améliorer la planification de la fourniture des approvisionnements
Introduction
La gestion de l'éternelle lutte entre un stock trop important et un stock insuffisant est au cœur d'une gestion efficace de la chaîne d'approvisionnement, mais c'est une équation que les organisations ne parviennent pas toujours à résoudre.
Il s'agit d'une situation typique : l'entreprise n'apprécie pas le montant des stocks qu'elle détient, aussi un décret est-il émis pour les réduire. La production est arrêtée jusqu'à ce que les stocks soient ramenés à un niveau acceptable, pour constater, quelques semaines plus tard, que les clients sont mécontents de ne pas pouvoir se procurer les produits qu'ils souhaitent. La production redémarre donc et tourne à plein régime pendant les mois suivants pour tenter de rétablir la situation de l'offre. Le résultat ? L'entreprise se retrouve avec un stock plus important qu'au départ.
Cependant, lorsqu'il s'agit d'optimiser les stocks, les choix vont bien au-delà du simple arrêt de la production. La réponse réside dans une planification efficace de l'approvisionnement. En analysant correctement les décisions qu'elle prend concernant les niveaux de service, les temps de cycle, l'utilisation de la capacité de production et le stock de sécurité, une organisation peut créer une liste d'options pour s'assurer qu'elle dispose toujours de la bonne quantité.
Plutôt que d'attendre que la prochaine âme courageuse arrête la production jusqu'à ce que les stocks soient épuisés et laisse l'histoire se répéter, un changement de paradigme est nécessaire.
Niveau d'inventaire optimal
Ce n'est que lorsqu'une entreprise peut définir les stocks dont elle a besoin pour gérer efficacement ses activités et atteindre ses objectifs, qu'elle peut s'attaquer au "monstre des stocks" et apporter des améliorations durables. Mais comment une organisation peut-elle décider du "bon" niveau ?
Il existe de nombreuses formules permettant de calculer le stock de sécurité d'une entreprise en fonction de la variation de l'offre et de la demande, des délais de livraison et du niveau de service que l'entreprise souhaite obtenir. Mais c'est la partie facile et avant de s'engager dans cette voie, l'entreprise doit prendre du recul et examiner les raisons pour lesquelles elle détient des stocks en premier lieu.
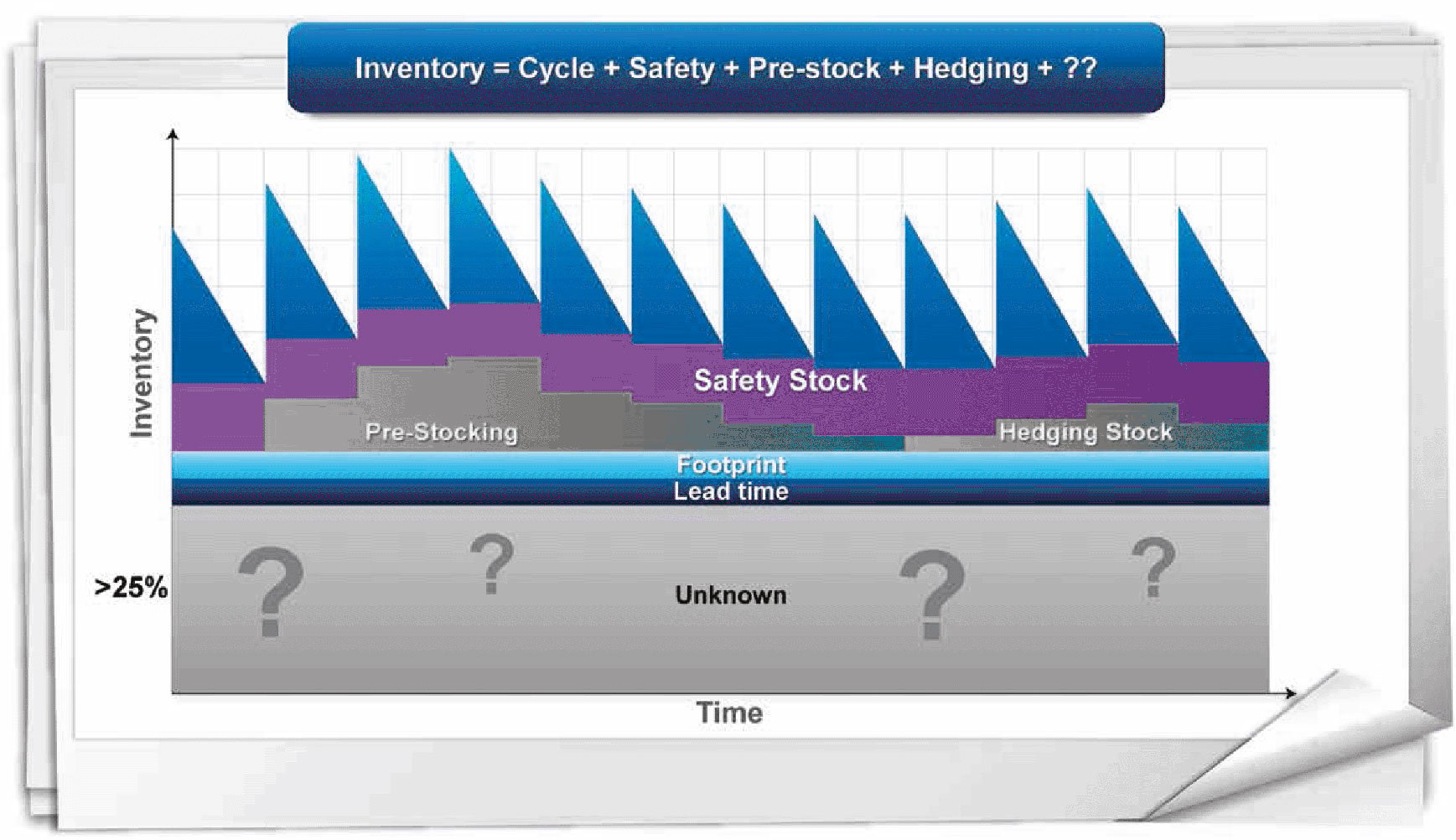
Trop souvent, une entreprise se précipite pour éliminer les stocks visibles (stock cyclique, stock de sécurité, pré-stockage et stock de couverture). Cependant, comme le montre la figure 1, c'est sur le reste - le grand invisibles - qui peut représenter jusqu'à 25 % des stocks d'une entreprise, que les efforts doivent se concentrer.
Cependant, il ne suffit pas d'éliminer d'un coup les stocks inconnus. Essayer de supprimer les stocks sans s'attaquer à la cause profonde, c'est comme s'attaquer aux symptômes d'une maladie avant le diagnostic. Il est essentiel de comprendre d'abord vraiment pourquoi il est là, puis de mettre en place un plan d'action bien réfléchi pour le supprimer.
L'inventaire en conséquence
Alors, comment les stocks sont-ils créés en premier lieu ? Il résulte des nombreuses choses qu'une entreprise fait ou laisse faire inconsciemment et qui peuvent être classées sous l'une des trois rubriques suivantes (comme le montre la figure 2) : variation et erreur ; inefficacité ; prise de décision stratégique et tactique. Une entreprise doit maîtriser chacun de ces éléments avant de pouvoir gérer efficacement ses stocks et, par conséquent, devenir à la fois légère et agile.
Une cause évidente des stocks est la variation entre l'offre et la demande ; dans un monde hypothétique où les organisations ont une précision de prévision de 100 pour cent, il n'y a pas besoin de stock de sécurité. Dans la réalité, bien sûr, les entreprises sont souvent en proie à des prévisions de la demande inexactes et trop zélées et se retrouvent donc avec trop de stocks. Les erreurs aussi - qu'il s'agisse d'acheter les mauvais matériaux, de produire des produits hors normes ou de mauvaise qualité, ou d'utiliser des données erronées dans les prévisions et la planification - entraînent des stocks inutiles.
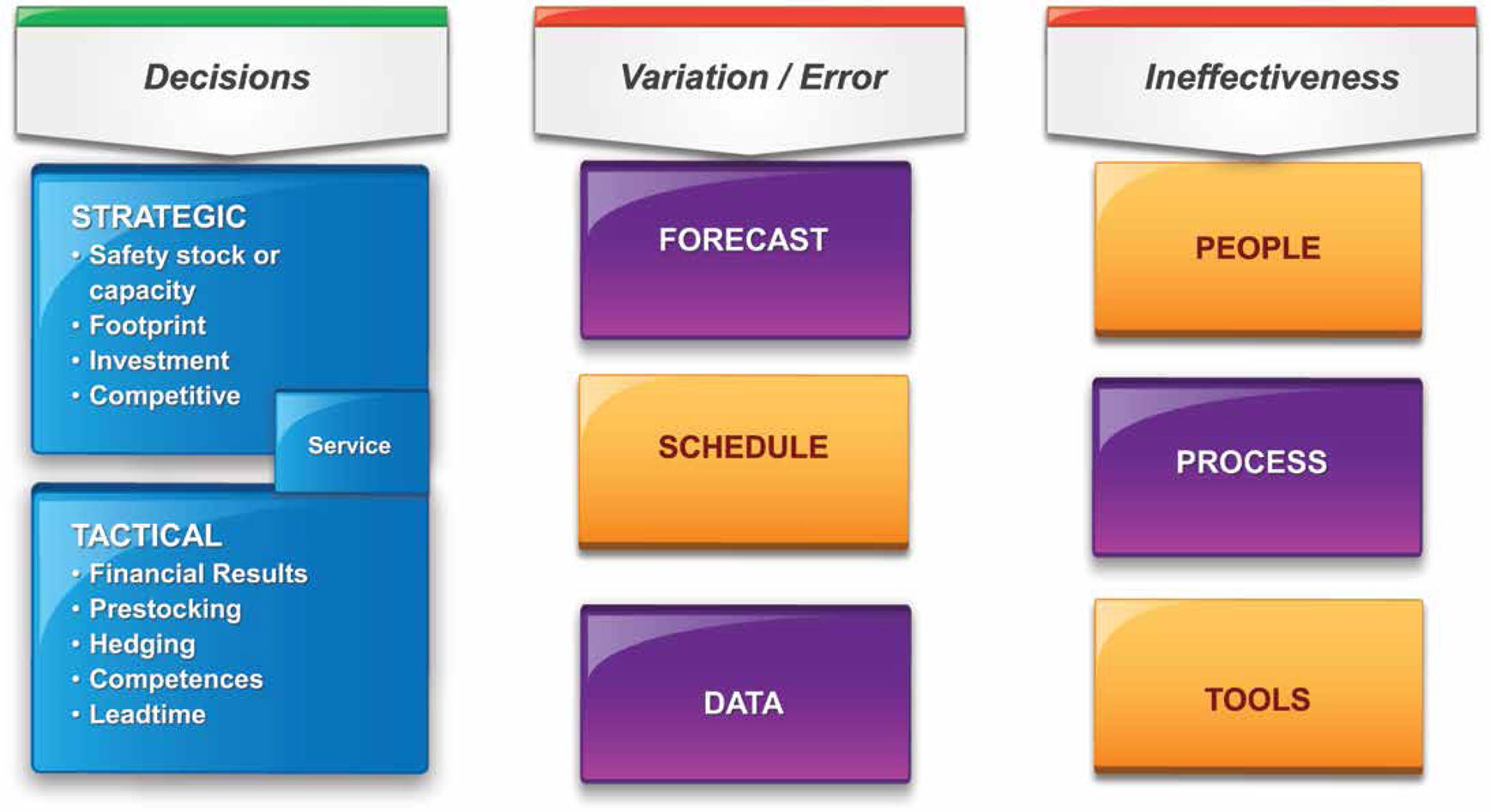
Les stocks créés en raison de l'inefficacité des personnes, des processus et des outils sont moins évidents. Un exemple courant : les entreprises qui ne disposent pas d'un système ERP (oui, il y en a encore beaucoup) et qui effectuent des calculs de type MRP sur une feuille de calcul ne le feront souvent que sur une base hebdomadaire ou mensuelle en raison du temps que cela prend. En conséquence, ces entreprises conservent souvent un stock de sécurité plus élevé "au cas où".
Plus fondamentalement, les stocks sont la conséquence des décisions stratégiques et tactiques prises par une entreprise ; les décisions concernant le nombre de points d'approvisionnement dans la chaîne d'approvisionnement, les niveaux de service requis, ou le niveau d'efficacité de fabrication nécessaire, ont toutes un impact énorme sur les stocks. Il est frappant de constater que les stocks qu'une entreprise détient aujourd'hui sont généralement la conséquence des décisions qu'elle a prises il y a plusieurs mois, années, voire décennies. Lorsqu'elles prennent ces décisions, les entreprises ne reconnaissent pas l'impact à long terme qu'elles ont sur les stocks, et fixent plutôt arbitrairement des objectifs sur la base d'un certain nombre de semaines de couverture. Les personnes impliquées dans les décisions quotidiennes relatives aux stocks ne comprennent pas ou ne contrôlent pas les leviers qui influent sur les objectifs de stocks, et la pauvre âme à qui l'on donne le titre de "gestionnaire des stocks" n'est souvent rien de plus qu'une gardienne de stocks, sans pouvoir réel d'influencer son existence.
Ne démontez pas les stocks, changez la façon dont ils sont gérés.
Une fois que la cause des stocks est comprise, il est temps de s'attaquer à la manière de les gérer. La planification intégrée de l'entreprise (S&OP avancée) peut fournir le contrôle des processus, la visibilité de la planification et la prise de décision efficace, qui sont essentiels pour bien gérer les stocks.
La planification intégrée des activités (PIA) est au cœur de nombreuses organisations. Il s'agit du processus de gestion qui permet de faire fonctionner l'entreprise, d'aligner les plans stratégiques et tactiques chaque mois et d'allouer les ressources essentielles - personnes, équipements, stocks, matériaux, temps et argent - afin de satisfaire les clients de la manière la plus rentable possible.
Au fur et à mesure qu'une entreprise développe son processus IBP, elle atteindra différentes phases de maturité, passant de la lutte contre les incendies et des processus de gestion déconnectés de la phase 1 au contrôle des processus d'entreprise de la phase 2. La figure 3 montre les améliorations qu'une entreprise doit apporter pour s'attaquer à la cause première des stocks tout au long de ce parcours de maturité.
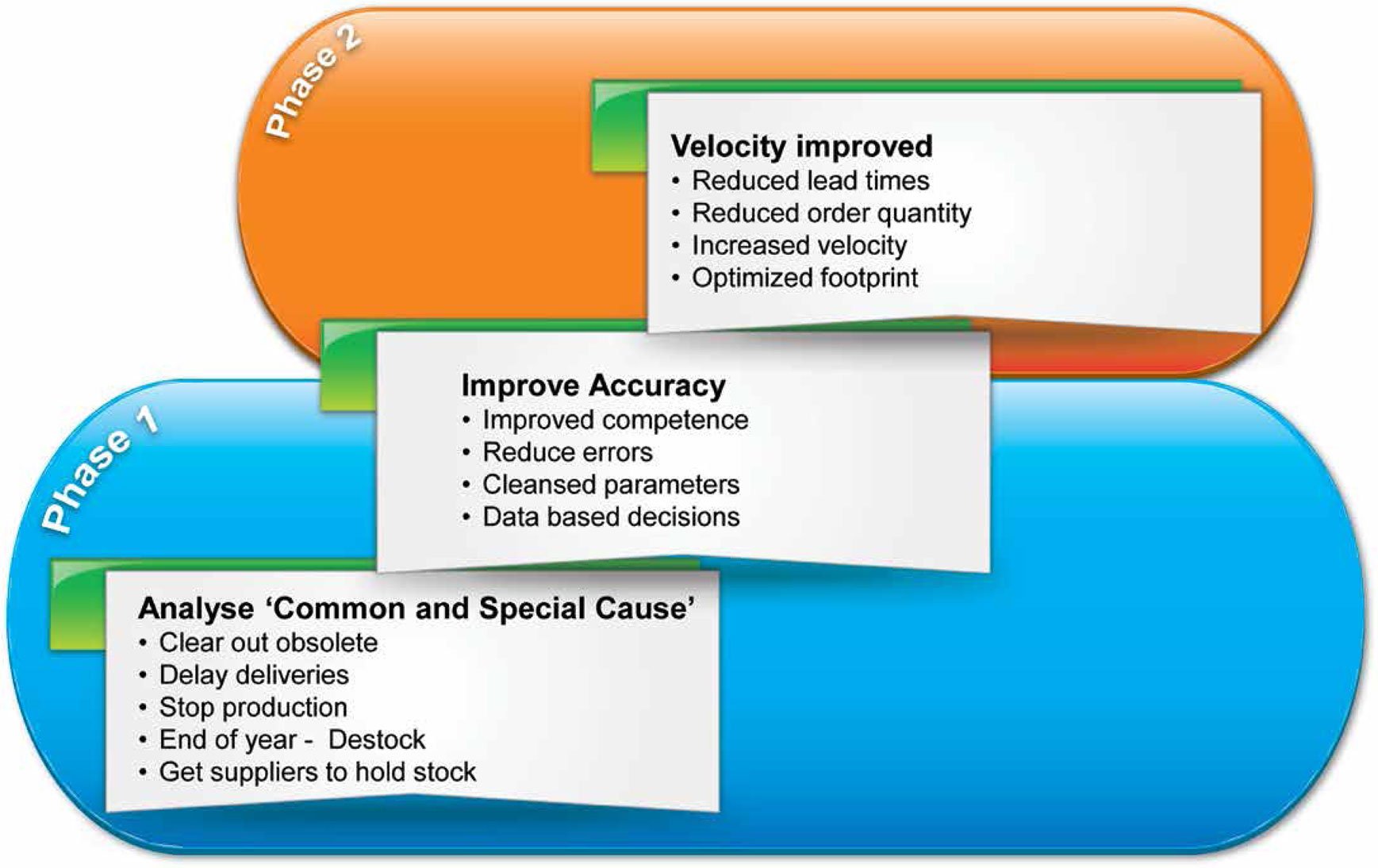
Dans la phase 1, il faut s'attaquer à l'inefficacité et à l'imprécision. Ici, les organisations doivent en priorité éliminer la variation - en supprimant les grosses erreurs de processus. Elles doivent avoir une bonne compréhension de leurs processus opérationnels et s'assurer qu'ils sont exécutés de manière cohérente. Pour qu'une entreprise atteigne le sommet de la phase 1, elle doit avoir le "contrôle" et faire tout ce qu'elle prévoit de faire, comme prévu, au moins 95 % du temps. Grâce à l'amélioration de la compréhension et de la planification qu'une organisation acquiert en phase 1, il est possible d'éliminer une grande partie de l'inventaire inconnu qu'elle détient.
Au sommet de la phase 1 vers la phase 2, les organisations commenceront à comprendre l'impact des décisions et à tenir compte de l'inventaire dans les décisions qu'elles prennent. L'IBP fournit à l'équipe dirigeante une vision claire des problèmes et des écarts entre les performances prévues, telles qu'elles sont définies dans les plans stratégiques/d'entreprise descendants, et la projection ascendante de la direction réelle de l'entreprise. L'IBP met l'accent sur la gestion des hypothèses et la planification des scénarios, afin de garantir que les décideurs envisagent toutes les alternatives possibles, pour pouvoir ensuite choisir ce qu'ils pensent être la meilleure alternative, en toute confiance.
Gestion de l'inventaire
Comme nous l'avons vu précédemment, lorsqu'il s'agit de prendre des décisions concernant les stocks, l'arrêt de la production est rarement la solution et les organisations doivent prendre en compte toutes les variables de l'offre pour gérer efficacement leurs stocks, en regardant au-delà de la fenêtre d'exécution immédiate avant de prendre des décisions critiques.
Niveau de service et stock de sécurité
Dès qu'une entreprise dépasse un niveau de service de 95 %, la quantité de stock de sécurité dont elle a besoin pour fournir ce service augmente considérablement. La figure 4 montre le facteur de multiplication qui s'applique dans le calcul du stock de sécurité, en fonction du niveau de service. Lorsqu'une entreprise fixe son objectif de niveau de service, elle doit soigneusement prendre en compte l'impact que cela a sur les stocks ; augmenter les niveaux de service implique de détenir davantage de stock de sécurité pour éviter de décevoir le client.
Il y a deux questions que les entreprises doivent se poser :
- Devons-nous vraiment offrir des niveaux de service de 100 % ?
- Sommes-nous conscients de ce qu'il en coûte de fournir des niveaux de service de 100 % et du stress que cela représente pour les gens ?
Dans un monde idéal, chaque organisation aurait un niveau de service de 100 % ; en réalité, beaucoup doivent se contenter de 95 %. L'analyse comparative de l'organisation et l'examen de ce que proposent les concurrents sont des conditions préalables essentielles pour déterminer ce qu'est un niveau de service acceptable. Regardez également ce que le marché attend.
Par exemple, 95 % peut être suffisant pour la plupart des industries, mais pour les industries pharmaceutiques et médicales, 95 % ne suffira pas. Dans le passé, les chaînes d'approvisionnement pharmaceutiques préféraient des niveaux de service élevés à l'agilité de la fabrication, en maintenant des niveaux de stocks et des coûts de possession élevés pour éviter les ruptures de stock. Mais avec l'augmentation des produits pharmaceutiques génériques par rapport aux produits brevetés et le coût élevé du développement des médicaments, la chaîne d'approvisionnement subit une pression énorme sur les prix. Par conséquent, il n'est plus acceptable pour les chaînes d'approvisionnement pharmaceutiques d'avoir des stocks excédentaires. Mais lorsque des vies peuvent littéralement dépendre de l'approvisionnement en produits, les produits pharmaceutiques doivent toujours viser des niveaux de service de 98 %, en construisant les chaînes d'approvisionnement autour d'une planification très précise de la demande.
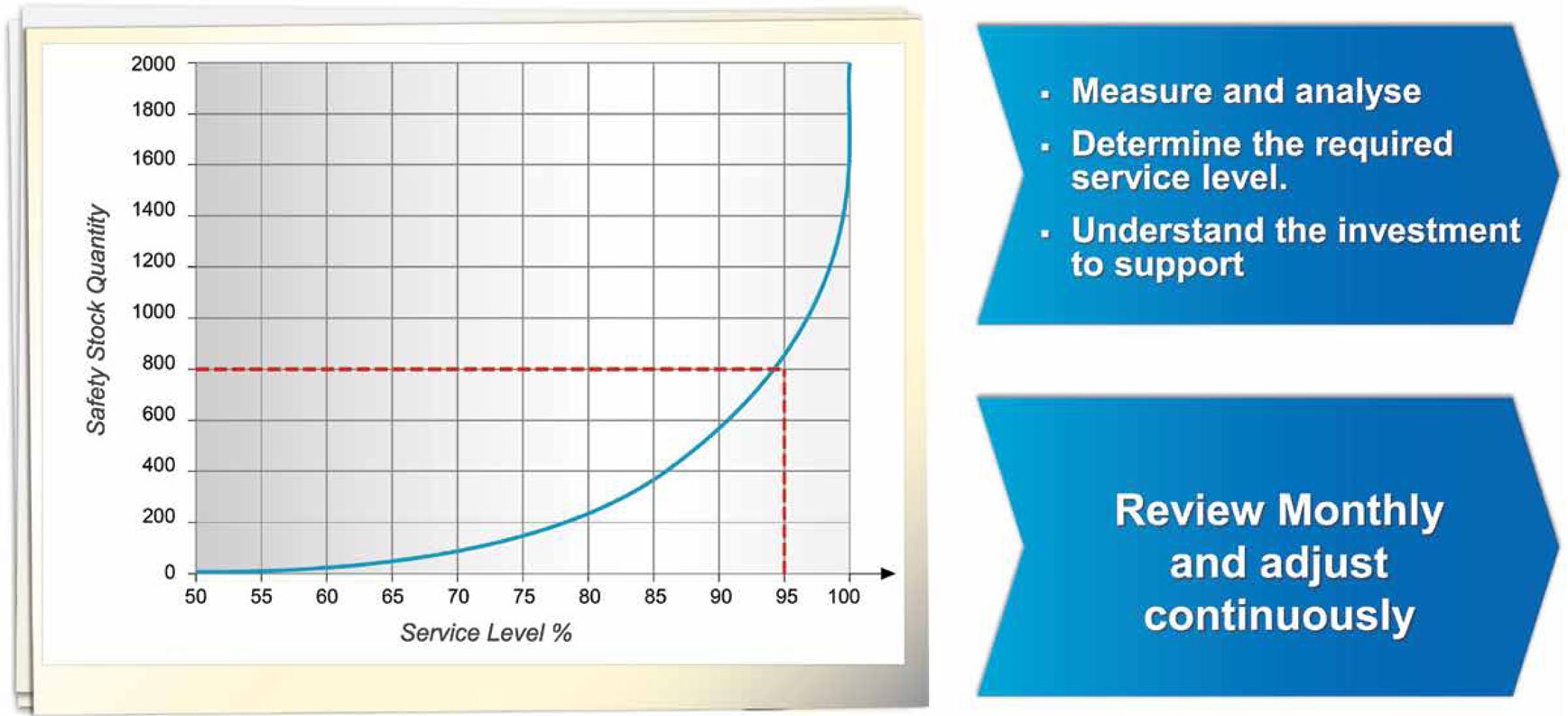
Ce type d'analyse de marché doit se faire entreprise par entreprise pour déterminer les niveaux de service que l'organisation peut se permettre.
Une organisation avec laquelle Oliver Wight a travaillé a été confrontée à la tâche de réduire les stocks de 25 pour cent. Pour ce fabricant mondial de produits chimiques, le fait de ne pas atteindre son objectif avait de graves conséquences financières. Il était clair que réduire la production sans changer les paramètres n'allait rien faire d'autre que de causer des problèmes d'approvisionnement. L'entreprise fonctionnait avec des niveaux de service de 98 % pour obtenir un avantage concurrentiel, mais en ramenant ce taux à 95 %, il était possible de réduire considérablement les stocks. La conséquence a été une légère augmentation du risque que certains clients ne reçoivent pas les produits à temps, mais ce risque a été largement compensé par les économies potentielles. Le résultat ? Une réduction du stock de sécurité d'une valeur d'un demi-million de dollars.
Réduction du temps de cycle
Une autre division de la même entreprise a été confrontée à un défi similaire de réduction des stocks. Mais ici, la solution était différente : la division menait de longues campagnes d'efficacité opérationnelle, mais en produisant deux fois moins, deux fois plus souvent, elle a vu une réduction substantielle du stock de cycle. Le risque était d'avoir des changements plus fréquents, mais en fin de compte, elle deviendrait plus agile dans sa réponse au marché. Et avec des temps de cycle plus courts, le risque d'obsolescence était moindre. Le stock cyclique a été réduit de 500 tonnes, avec une réduction supplémentaire de 150 tonnes du stock de sécurité, soit une réduction impressionnante de 40 % du stock total pour ce groupe de produits.
Gestion de la capacité de sécurité
La plupart des organisations considèrent les stocks comme leur seule option pour pallier les mauvaises performances d'approvisionnement et leur donner la flexibilité nécessaire pour satisfaire une demande imprévue. Mais en fait, investir dans la capacité de sécurité, dans le cadre de la stratégie d'approvisionnement, peut être une option plus économique. Plutôt que de considérer que l'objectif de l'organisation est de maximiser l'utilisation des actifs et de faire fonctionner l'usine à 100 % de sa capacité, réduire son utilisation à 90 % et avoir la capacité de l'augmenter lorsque la demande l'exige, peut réduire la quantité de stock nécessaire. La fabrication flexible réduit en fin de compte l'investissement, les coûts permanents et les risques associés à la détention de stocks excédentaires.
Gestion du stock de sécurité
Normalement, par manque de compréhension de la véritable variation de l'offre et de la demande, de nombreuses entreprises disposent d'un stock de sécurité générique de deux semaines pour chaque produit de leur portefeuille. Mais il est important de considérer l'importance de chaque produit. Ceux qui sont plus stratégiques ou dont les exigences des clients sont plus strictes (voire contractuelles) peuvent nécessiter des niveaux de service plus élevés et donc des stocks plus importants. Considérez également les produits dont la demande varie si peu que le stock de sécurité est à peine nécessaire car les besoins peuvent être prédits avec une grande précision. Si le stock de sécurité n'est jamais utilisé, pourquoi en avoir ? La règle simple est de constituer des stocks là où ils aident l'entreprise et de les réduire là où ils sont excédentaires.
Un changement culturel
En changeant la façon dont les stocks sont gérés, il y aura des problèmes de comportement et des silos fonctionnels à surmonter. Souvent, c'est la fabrication qui dicte la quantité à produire plutôt que la production qui est basée sur les besoins de l'entreprise. De même, la demande impose souvent des prévisions élevées pour s'assurer que les clients reçoivent leurs commandes à temps.
Méfiez-vous de ce préjugé dans les affaires ; il tue les chaînes d'approvisionnement et peut tuer les entreprises. Heureusement, il est possible de l'éviter. En confiant à la demande et à l'offre la responsabilité conjointe des stocks, les entreprises peuvent améliorer la précision des prévisions. Cette prise en charge conjointe implique toutefois un changement culturel : il s'agit de faire tomber les barrières entre les départements, d'éliminer la culture du blâme et de créer un environnement basé sur le travail d'équipe, où tout le monde est aligné sur la stratégie.
La planification intégrée des activités permet de s'attaquer à ces paradigmes car elle démolit les barrières organisationnelles traditionnelles et crée une structure basée sur des processus intégrés.
Le défi consiste à mettre en œuvre un programme de gestion du changement parallèlement à la planification intégrée des activités, afin de modifier les comportements et de tirer pleinement parti des avantages des processus et des équipes intégrés. Les gens doivent savoir clairement quels sont leurs rôles et leurs responsabilités. En ce qui concerne les stocks, de nombreuses personnes sont impliquées ; les influenceurs essentiels sont ceux qui ont un impact sur les finances, les risques, le service, les délais, l'empreinte, le stock cyclique, la fréquence de planification et le stock de sécurité. Identifier ces acteurs clés et les doter des connaissances nécessaires leur permet d'appliquer les meilleures pratiques dans le cadre de leurs rôles et responsabilités clairement définis. Les personnes sont l'arme la plus puissante de l'organisation pour une gestion efficace des stocks et pour créer une entreprise légère et agile.
Conclusion
La gestion des stocks n'est pas une question à laquelle il faut s'attaquer uniquement lorsqu'un problème majeur survient. Alors que les chaînes d'approvisionnement deviennent plus longues et plus complexes, et que la volatilité économique mondiale persiste, il est essentiel de prendre le contrôle des stocks pour répondre de manière rentable aux exigences du consommateur d'aujourd'hui.
Avec un processus de planification intégrée des activités en place, une entreprise disposera du contrôle, de la visibilité et de l'aide à la prise de décision efficace dont elle a besoin pour gérer ses stocks.
La prise en compte de toutes les variables de l'offre, à savoir les niveaux de service, les temps de cycle, l'utilisation de la capacité de production et le stock de sécurité, permettra de dresser une liste d'options judicieuses pour la gestion des stocks. Ainsi, au lieu de simplement arrêter la production, l'organisation peut prendre des décisions éclairées, prévoir avec plus de précision le stock total dans la planification à long terme et viser continuellement des réductions.
En fin de compte, changer la façon dont les stocks sont gérés contribuera à créer une entreprise légère et agile.